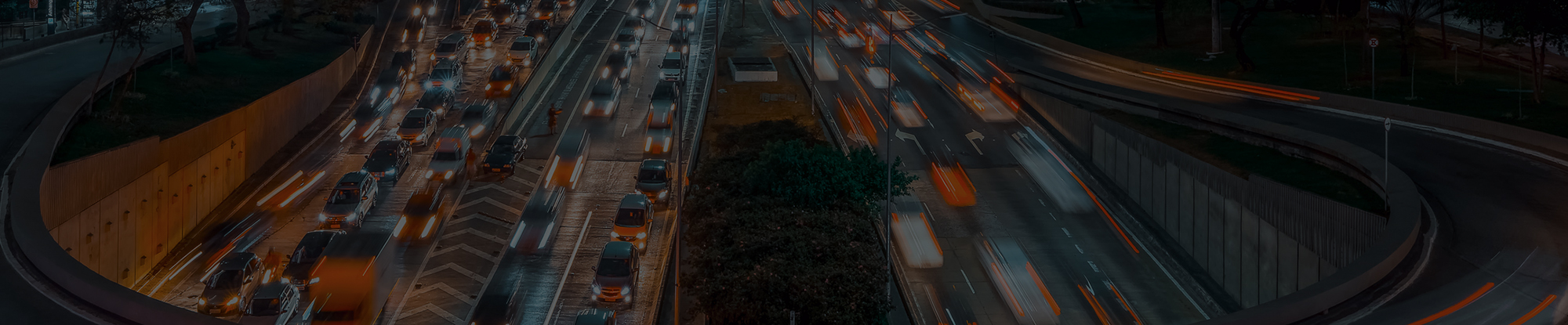
Epic Resins' Automotive Solutions: Adhesives, Potting & Encapsulating Compounds
Epoxy Resins and Polyurethanes for Automotive Manufacturing
Epic Resins offers innovative adhesives, potting and encapsulating compounds designed specifically for the automotive industry. With a portfolio tailored to meet the diverse needs of automotive manufacturers, we provide solutions that enhance performance, durability, and safety. Make Epic Resins your automotive resin supplier for your next project.
Precision Adhesives for Automotive Engineering
Our precision-engineered adhesives deliver exceptional bonding strength, offering solutions for various automotive applications. Whether for lightweight construction, robust connections, or intricate assemblies, Epic Resins' adhesives guarantee quality and performance.
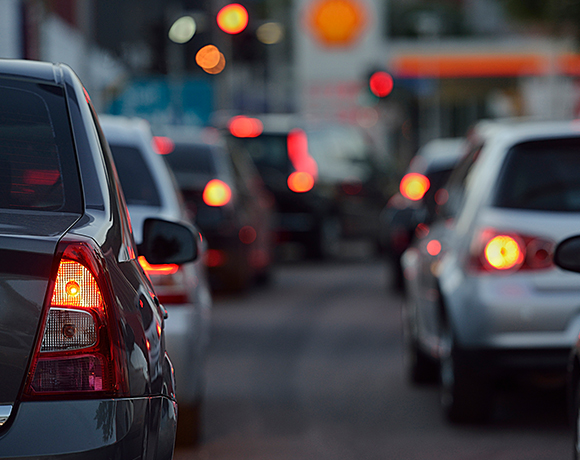
Epic Resins: Your Automotive Resin Supplier
From Utility vehicles to high-performance sports cars, Epic Resins offers automotive epoxies and polyurethanes that redefine industry standards. We provide tailored solutions to meet your specific needs.
The Role of Epoxy Resins and Polyurethanes in Ignition Systems
The auto industry uses epoxy resins and polyurethanes in coil assemblies within the ignition systems. Potting or casting the metal coil with a compound helps protect it from the elements. A reliable compound insulates the auto coil ensuring complete protection against moisture, chemicals, wear, and foreign elements.
Here are several ways having a quality potting compound will improve your coil assembly:
- Protection against vibration
- Electrical Insulation
- Resistance to corrosives and other environmental hazards
- Electrical potting for impregnation of high-voltage coils
- Thermal shock resistance
- Moisture protection
Epoxies and Polyurethanes Designed for Automotive Ignition Coils
Epic Resins formulates and manufactures potting and casting compounds designed specifically for automotive functions. Key features include:
- Shelf Stability Formulated to remain strong and effective with a long shelf life.
- Low Hardness Offers flexibility when needed in the auto coil assembly.
- Low Viscosity Allows the resin to flow better onto the coils.
- Thermal Resistances Protect your ignition coils from extreme temperatures weather year-round.
- High Dielectric Strength Withstand high voltages without breaking down.
- Flame Retardant Slow or stop a fire when exposed to flames.
Intelligent Resins for Electric and Hybrid Vehicles
As electric and hybrid vehicles become increasingly prevalent, Epic Resins delivers specialized automotive adhesive, potting, and encapsulating solutions that meet unique challenges that enhance overall vehicle performance.
Quality Assurance and Compliance
Epic Resins adheres to international automotive standards, reflecting our deep commitment to quality, safety, and reliability. Our resins undergo rigorous testing to ensure optimal performance under varying automotive conditions, such as thermal cycling, vibration and chemical exposure.
Formulated Solutions for Innovative Automotive Applications
Epic Resins offers automotive polymers for modern automotive technologies, including autonomous driving systems and smart sensors. Our products ensure seamless integration, enabling innovations that define the future of automotive technology.
Our automotive materials are distinguished by properties that cater to industry-specific needs, such as thermal stability, vibration control, and chemical resistance. With a focus on quality and innovation, our products offer solutions that set new benchmarks in automotive manufacturing.
Popular Formulations For The Automotive Industry
Epic S7214 is a two-component polyurethane potting/casting compound. S7214 has been designed with a fast gel time and rapid hardness development. This potting material has extraordinary electrical insulation properties combined with advanced protection against corrosive elements and vibration. This polyurethane potting compound has been formulated for applications where excellent chemical resistance at ambient and elevated temperatures is an important design criterion. When mixed, S7214 results in dark green colored castings.
ProPreg E240 has the highest industry adhesion wire-to-wire, wire-to-aramid paper, aramid paper-to-steel and wire-to-low energy plastic slot liners. This single component epoxy secondary insulation has a high operating temperature and quick cure.
Epic 0218EV is a single-component epoxy adhesive and potting compound. Epic 0218EV is designed to have excellent bonding and thermal properties and features a 10-month shelf life at 25°C.
Epic 0227 is a single component, 100% solids epoxy potting compound. It is designed to have a high thermal conductivity and a high Tg for thermally demanding applications. This component is designed to pass UL 94 V-0 and have a CTE below 30 ppm.
Epic S7591 is a two-component epoxy that is designed for high temperature applications. It features a low thermal expansion rate coupled with a high glass transition temperature. S7591 is also designed to provide an extremely high 3 W/mK thermal conductivity for rapid removal of heat generated by electrical/electronic components.
Epic S7592 is a two-component polyurethane adhesive designed to pass UL 94 V-0 flame retardancy testing. This urethane has been formulated to provide superior adhesion to a variety of substrates, including plastic and metal.
Frequently Asked Questions (FAQs)
What range of automotive applications do Epic Resins' products cater to?
Epic Resins formulates and manufactures adhesives, potting, and encapsulating compounds designed for a wide array of automotive applications, and cutting-edge technologies like autonomous driving systems and smart sensors.
How does Epic Resins contribute to the sustainability of the automotive industry?
Epic Resins focuses on solutions that not only contribute to fuel efficiency but also support environmentally responsible manufacturing practices.
How does Epic Resins ensure quality and compliance in its automotive products?
Epic Resins adheres to international automotive standards and emphasizes quality, safety, and reliability. Rigorous testing ensures optimal performance under various conditions such as thermal cycling, vibrations, and chemical exposures.
Can Epic Resins provide customized solutions for specific automotive needs?
Yes, Epic Resins specializes in offering, customized solutions for modern automotive technologies. Our products enable seamless integration, catering to specific needs and enabling innovations that define the future of automotive technology.
How does Epic Resins support the electric and hybrid vehicle segment?
Epic Resins delivers specialized epoxy and polyurethane solutions for electric and hybrid vehicles, providing optimal bonding, insulation, and protection. These products enhance overall vehicle performance, catering to the unique challenges of this growing segment.
Partner with Epic Resins: Driving the Automotive Revolution
The automotive industry presents complex challenges, and at Epic Resins, our experience provides the insights, guidance, and solutions to navigate them successfully. Reach out to our team of experts and take your automotive projects to the next level with confidence and clarity.